Along with details on the 2016 Nissan Leaf, Nissan published a video showing us details of the battery pack factory in Smyrna Tennessee. This video happens to show construction of the new 30 kiloWatt-hour battery pack, which we know simply because of the shape of each module. And it happens to show us some interesting details about the Leaf battery pack innards.
The video is at the bottom. I’ve made a few screen captures to walk through what is shown.
The Nissan Leaf pack is not a regular rectangular shape, and it never has been. Some modules are laid horizontally, probably so they’ll sit under the seating area. Another group of modules are laid vertically, probably to fit behind the rear seats.
The new modules for the 30 kWh pack is packaged as 8 cells, in a 2P 4S arrangement. (2 in parallel, 4 in series)
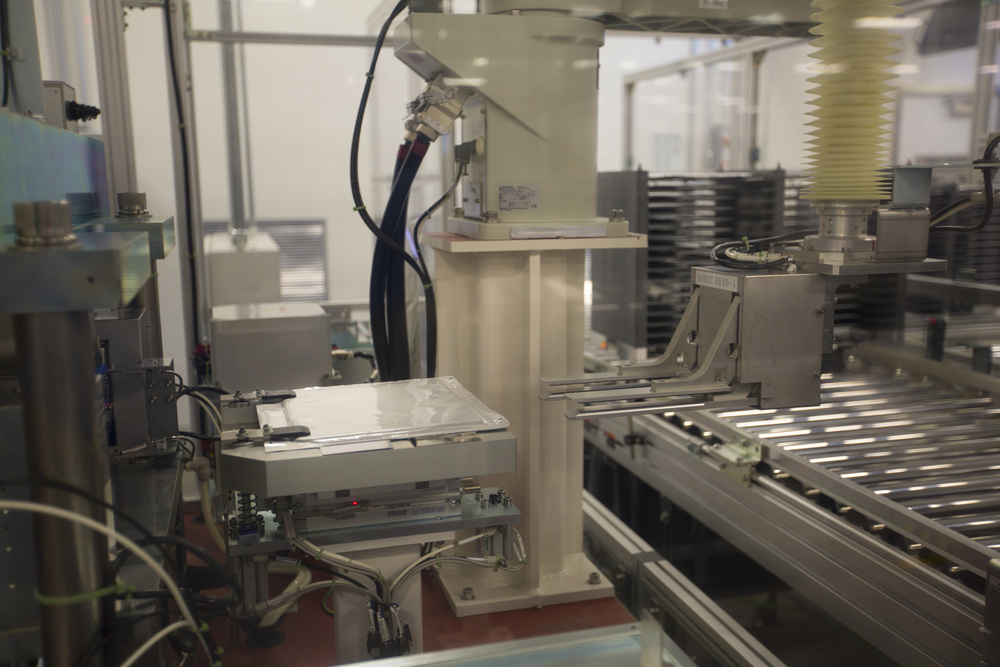
Battery cells traversing the machinery. Each cell is a pouch, with two tabs for the positive and negative connections.
It looks like the machinery is checking battery cell voltage – which would be a necessary step to weed out bad cells.
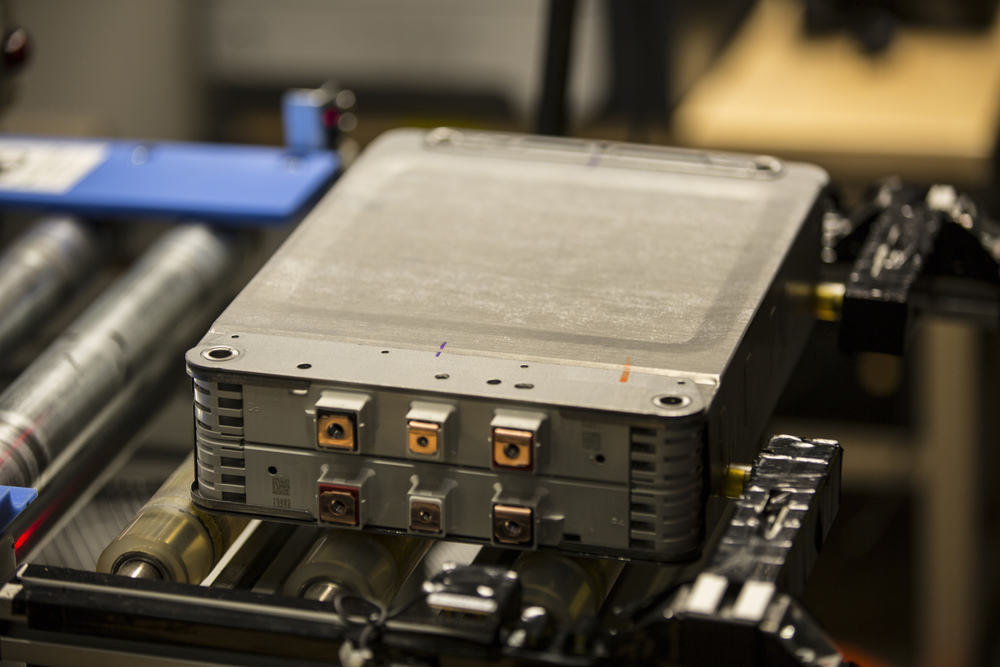
Battery module on the assembly line. Where the previous modules (for the 24 kWh packs) had single-height modules, this is a double-height module.
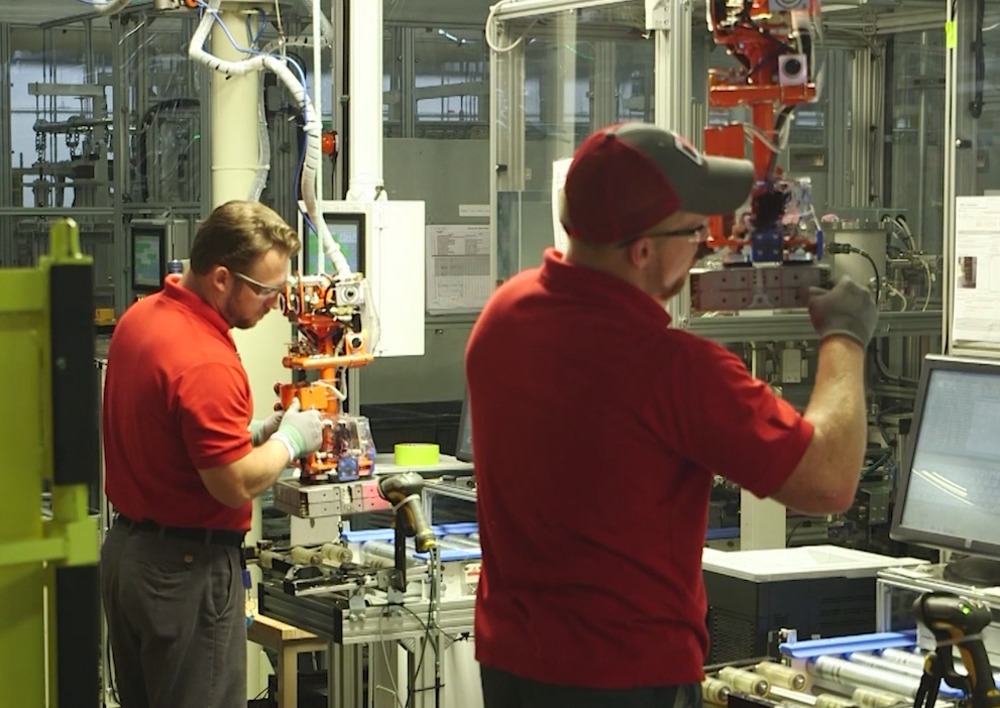
Another view of the module inspection process. It’s clear from the video the modules are held aloft by suction force, so the workers can inspect on all sides and the bottom.

Another angle to look closely at the battery modules. You’ll also notice a magic marker in his hand, that in the video is used to make marks that probably indicate the visual inspection was performed.

Assembling the battery pack. Lowering the group of modules into the pack, and preparing to wire everything together.
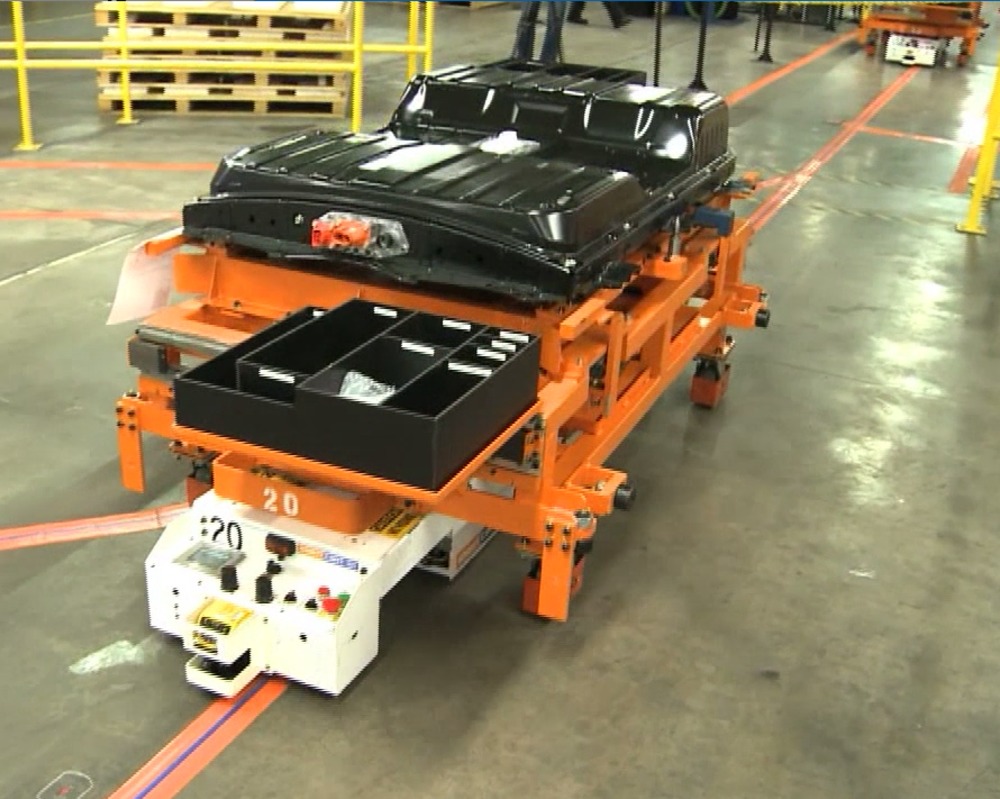
Finished battery pack on a trolley going to who-knows-where. The video shows that this trolley is robotic, and is probably following the orange lines painted on the floor.
- Is there enough Grid Capacity for Hydrogen Fuel Cell or Battery Electric cars? - April 23, 2023
- Is Tesla finagling to grab federal NEVI dollars for Supercharger network? - November 15, 2022
- Tesla announces the North American Charging Standard charging connector - November 11, 2022
- Lightning Motorcycles adopts Silicon battery, 5 minute charge time gives 135 miles range - November 9, 2022
- Tesla Autopilot under US Dept of Transportation scrutiny - June 13, 2022
- Spectacular CNG bus fire misrepresented as EV bus fire - April 21, 2022
- Moldova, Ukraine, Georgia, Russia, and the European Energy Crisis - December 21, 2021
- Li-Bridge leading the USA across lithium battery chasm - October 29, 2021
- USA increasing domestic lithium battery research and manufacturing - October 28, 2021
- Electrify America building USA/Canada-wide EV charging network - October 27, 2021